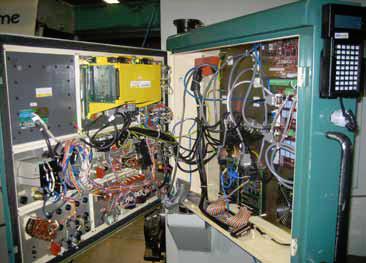
Thomas R. Cutler explains the benefits of automated overall equipment effectiveness data in a lean manufacturing environment.
Manufacturers are facing competitive price pressure, shrinking brand loyalty, and increasing costs. Compliance constraints are impacting business efficiencies while quality expenditures continue to increase. According to John Rattray, a principle of Memex Automation, “the only options to battle these trends are to increase efficiency, improve quality, while reducing fixed costs and lowering cost-of-goods sold (COGS).”
One way to implement this type of quality initiative is a cost management platform. Another option is to track the true overall equipment effectiveness (OEE) on the plant floor. A ten percent improvement in OEE can generate a greater than 60 percent increase in operating income, a tremendous increase to the bottom line that could represent over $5 million on sales of $100 million.
The speed of complex machine changeovers has a substantial effect on the profitability of a production run, but manufacturing line workers are often not encouraged to measure effectiveness, and profitability suffers accordingly.
Built-in intelligence goes beyond raw data collection to provide a fully integrated production and quality performance management application. The quality component for manufacturers is the ability to differentiate and compare real-time data against planned estimates. These discrepancies allow estimates to be validated and automation processes to be quantified.
Overall equipment effectiveness
Overall equipment effectiveness (OEE) is critical to quality control, directly measures productivity (actual production compared to capacity to produce), and is correlated directly to operating income and profit.
Production machines are designed on the basis of a certain production capacity. In practice, actual output lags far behind the capacity of the equipment, for a number of reasons, meaning that there is hidden production capacity.
The business case for OEE is very sound. In the book, Overall Equipment Effectiveness: A Powerful Production/Maintenance Tool for Increased Profits by Robert C. Hansen, on pages 47-56 he compares the business case of a 10 percent improvement in OEE for a manufacturer producing and selling $100 million per year, generating an EBIT of $9 million. The base business case of operating at a 60 percent OEE is compared to the same company operating at a 66 percent OEE. Firstly, comparing the reduction of direct labor's impact to operating income—a 21 percent improvement in EBIT; secondly, comparing the impact of increased sales to operating income—a 62 percent improvement to EBIT.
Machine performance is always in comparison to an ideal machine—specifically a machine which always operates at maximum speed and with a quality rate of 100 percent. OEE is determined by losses in availability, performance, and quality. The OEE indicates how effectively a machine is being used compared to the ideal machine (OEE = 100%). World class OEE is considered to be 85 percent, made up of 95 percent each of availability, performance, and quality.
Specific measurable results can be realized from OEE technology solutions while it remains a simple and easily understandable tool for improvement.
· OEE solutions automatically and quickly identify the problem (make them visible)
· Prioritization of processes to improve becomes clear very quickly
· The ability to make well-founded choices for specific improvements is factually (data) based
· OEE increases are a direct result of the improvements and can be observed immediately.
"Most manufacturers like to believe they are operating at a high efficiency level according to traditional methods of measurement using operator collected data,” said Rattray. “But many executives and engineers feel there is much room for improvement on the shop floor, but have difficulty getting actual data to support their case. When using a world class metric of productivity like OEE, manufacturers often discover that they are operating at only fifty percent of operating efficiency.” By automatically collecting OEE from the machines, a company can apply the paradigm “if you can measure it, then you can manage it.” Exposing the plant team to the three components of OEE—quality, performance, and availability—they become able to focus on the most critical issues that produce real benefits for the company.
When OEE data is captured directly at the machine, the concept also becomes accessible to the machine operators (the employees who have the most to gain from tracking and improving the effectiveness of the operating equipment).
OEE and lean
Blount is a discrete manufacturer specializing in chain saw components. At its plant in Guelph, Ontario, the company operates a 1,200 machine facility and serves a global market. Manufacturing executives were looking for a performance management solution to support the company's lean initiatives and needed to find a means to improve production reporting accuracy, reliability, and frequency.
The company had a particular machine that was only performing at 30 percent OEE, backlogged with 1,000s of parts, downstream production starved, a classic bottleneck affecting overall plant production.
Blount sought a technology solution to help identify the exact cycle time of the machine and gain insight into the process flow (as well as the decision-making flow). Memex Automation offered OEE quantification metrics directly at the machine through hardware and software. Within 48 hours of the implementation the manufacturing engineers were able to reduce waste relative to downtime, labor, energy and raw materials and increased OEE by 100 percent. The technology enabled real-time production reporting for more reliable and accurate data as well as significantly increasing visibility into day-to-day operations with a resultant benefit of increased collaboration between operators, engineers and production.
The primary challenge was to eliminate aspects of the manufacturing process that did not add value to customers. The application of lean principles, including value stream mapping, together with accurate OEE data, was central to the success of the project.
In another case, excessive waste resulting from unplanned downtime and over-consumption of raw materials necessitated drastic changes at Rose Integration Ltd., a Carleton Place, Ontario precision machined components manufacturer. Based on historical data, annual unplanned downtime amounted to 25 percent of the aggregate of all production lines. Taking the cost of labor, quality, and lost production time into account, the shortfall represented hundreds of thousands of dollars in lost opportunity.
Over and above the cost of downtime, waste due to over-processing translated to excess energy consumption and chemical usage. While parts on the line waited to move from one process to the next, energy was wasted. The company had also grown and had run out of physical space; the project increased production capacity by 25 percent, and was more than paid for by saving the cost of buying new machines and the huge extra benefit of not having to expand the plant.
At the end of every shift, employees would physically count the number of parts produced and enter the figures into a spreadsheet manually. By automating the process, accurately, direct from the machine, the operators were freed to do other tasks.
"To stay competitive, we needed to invest in lean technology to provide customers with the best possible service,” said Graham Whitelaw, president of Rose Integration Ltd. “Since implementing the OEE solution we have clearly identified the root causes associated with unplanned downtime and as a result we were able to reduce total downtime by 25 percent. We also improved our material flow by lowering the incidence of machine stoppages and are better able to manage energy use and keep the costs of quality down to a minimum. The ROI on implementing this solution over all the machines had a payback of less than three months."
In Progressive Inc.'s Arlington, Texas facility, real-time reporting accuracy and reliability gave way to a number of other capabilities. Automatic event detection and escalation allowed supervisors and managers to keep on top of issues as they arose, rather than after the fact. Better product quality resulted from more efficient use of materials; total operational visibility into production provided managers with access to decision support information from anywhere in the plant.
“Not all OEE technologies are created equally,” said Rattray. “Many are inefficient manual systems, involving operator input on a clipboard, re-keying into a spreadsheet. An intelligent performance management system getting signals direct from the machine is designed to increase operational efficiency, accuracy, improve quality, and drive higher levels of performance in manufacturing and other production operations.”
* * *
Thomas R. Cutler is president & CEO of Fort Lauderdale, Florida-based, TR Cutler, Inc., and founder of the Manufacturing Media Consortium of journalists and editors writing about trends in manufacturing. www.trcutlerinc.com